“Today, in the transformers market and especially in marine & offshore applications, a new trend is gradually solidifying: the use of eco-friendly technology with fully environmentally compliant transformers that are recyclable and non-polluting, which can be used in outdoor applications for which companies typically use oil-based solutions.
A very clear tendency in this context is the use of electric ferries. These ferries typically carry batteries that must be charged quickly in port and withstand the entire journey to the port of arrival.
The required transformers are very special, and typically have several secondaries with particular impedances and a need to withstand large loads for short periods of time.
TMC Transformers has participated in designing and manufacturing transformers in several such projects during the last two years in combination with engineering by several important ship designers. All this is complemented by a dedicated and expert service department. Repair operations on board are sometimes complex and often urgent, so the personnel dedicated to this task need to be top-notch. 24/7 availability is a must.
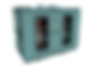
Moreover, the marine sector is very demanding, not only technically, but also in terms of project management. Professionals are required to have extensive experience in this highly specialized area.
Technically, this market is heavily regulated by several standards and certifications that managers must understand perfectly. In addition to the design itself, structural analysis using a finite element approach helps to verify the feasibility of the proposed solutions.
One feature differentiating marine transformers is the type of cooling. This influences not only the size and weight of the final solution, but also its efficiency and resistance to failure. The most common types of cooling are Air Natural (AN), in which the transformer does not require external cooling, and Air Forced – Water Forced (AFWF), where the transformer requires a highly specialized air-water heat exchanger integrated in its enclosure, where water is used to cool the air inside and therefore also the transformer coils.
Another common characteristic is the use of integrated pre-magnetization transformers to help with inrush currents that can damage the main transformer.
Lastly, given the environment where these transformers must operate, proper corrosion protection (metal treatments and painting) is necessary.”